How to polish stainless steel pipe?
The following seven methods of polishing stainless steel pipe are commonly used.
1. Mechanical polishing
2. Chemical polishing
3. Electrolytic polishing
4. Ultrasonic polishing
5. Fluid polishing
6. Magnetic polishing
7. Chemical mechanical polishing
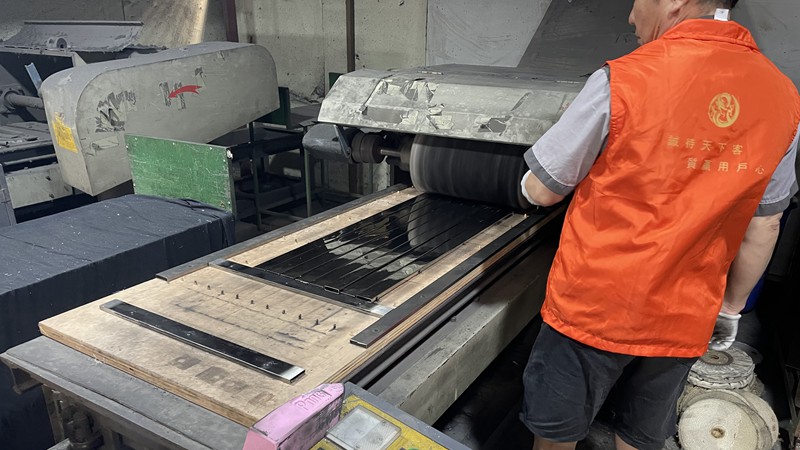
1. Mechanical polishing
Mechanical polishing is by cutting, material surface plastic deformation to remove the convex part of the polished and get a smooth surface polishing method, the general use of oil stone, wool wheel, sandpaper, etc., mainly by hand, special parts such as the surface of the rotary body, can use the rotary table and other auxiliary tools, the surface quality requirements of high can be used to ultra-precision polishing method. Ultra-precision grinding and polishing is the use of special abrasives, containing abrasives in the grinding and polishing fluid, pressed on the surface of the workpiece being processed, for high-speed rotary motion. Using this technology can achieve Ra0.008μm surface roughness, is the highest among various polishing methods. Optical lens mold often use this method.
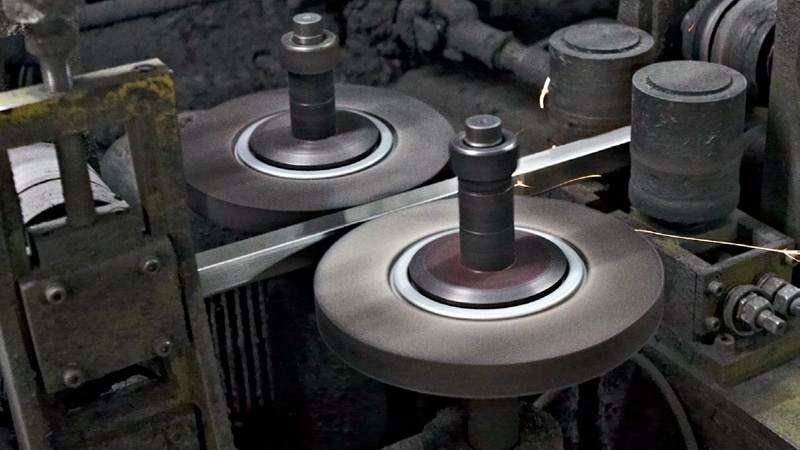
2. Chemical polishing
Chemical polishing is to let the material in the chemical medium surface microscopic convex part than the concave part of the priority dissolution, so as to get a smooth surface. The main advantage of this method is not complex equipment, can polish the shape of complex workpieces, can polish many workpieces at the same time, high efficiency. The core problem of chemical polishing is the preparation of polishing solution. Chemical polishing to get the surface roughness is generally a few 10μm.
3. Electrolytic polishing
The basic principle of electrolytic polishing is the same as chemical polishing, that is, by selective dissolution of the material surface tiny projections, so that the surface is smooth. Compared with chemical polishing, can eliminate the impact of cathodic reaction, the effect is better. Electrochemical polishing process is divided into two steps: (1) macro-leveling dissolution products to the electrolyte diffusion, the material surface geometric roughness decline, Ra>1μm.(2) micro-light leveling anodic polarization, surface brightness increase, Ra<1μm.
4. Ultrasonic polishing
The workpiece is put into the abrasive suspension and placed in the ultrasonic field together, relying on the oscillation of ultrasonic waves to make the abrasive grinding and polishing on the surface of the workpiece. Ultrasonic processing macro force is small, will not cause deformation of the workpiece, but the tooling production and installation is more difficult. Ultrasonic processing can be combined with chemical or electrochemical methods. On the basis of solution corrosion, electrolysis, and then apply ultrasonic vibration to agitate the solution, so that the workpiece surface dissolution products from the surface, corrosion or electrolyte near the surface evenly; ultrasonic cavitation in the liquid can also inhibit the corrosion process and facilitate the surface brightening.
5. Fluid polishing
Fluid polishing is to rely on the high-speed flow of liquid and the abrasive particles carried by the workpiece surface to achieve the purpose of polishing. Commonly used methods are: abrasive jet processing, liquid jet processing, fluid power grinding, etc. Fluid power polishing is driven by hydraulic pressure, so that the liquid medium carrying abrasive particles flowing over the surface of the workpiece at high speed reciprocally. The medium is mainly used in the lower pressure flow through the good special compounds (polymer-like substances) and mixed with abrasives, abrasives can be made of silicon carbide powder.
6. Magnetic grinding and polishing
Magnetic grinding and polishing is the use of magnetic abrasives in the magnetic field under the action of the formation of abrasive brushes, grinding and processing of the workpiece. This method has high processing efficiency, good quality, easy to control the processing conditions, and good working conditions. Using suitable abrasives, the surface roughness can reach Ra0.1μm.
7. Chemical mechanical polishing
Chemical mechanical polishing technology combines the advantages of chemical and mechanical grinding, is now the most commonly used polishing method, even cell phone cases, take the card pin, keys, etc. are polished with Jin Xin plane grinding machine. It can guarantee the efficiency of material removal while obtaining a more perfect surface, and the flatness obtained is 1-2 orders of magnitude higher than simply using these two kinds of grinding, and can achieve surface roughness from nano-level to atomic level. And the mirror effect out of polishing is very high brightness, no fault and good flatness. Generally with Jinxin plane grinding machine can achieve fast and good results.
1. Mechanical polishing
2. Chemical polishing
3. Electrolytic polishing
4. Ultrasonic polishing
5. Fluid polishing
6. Magnetic polishing
7. Chemical mechanical polishing
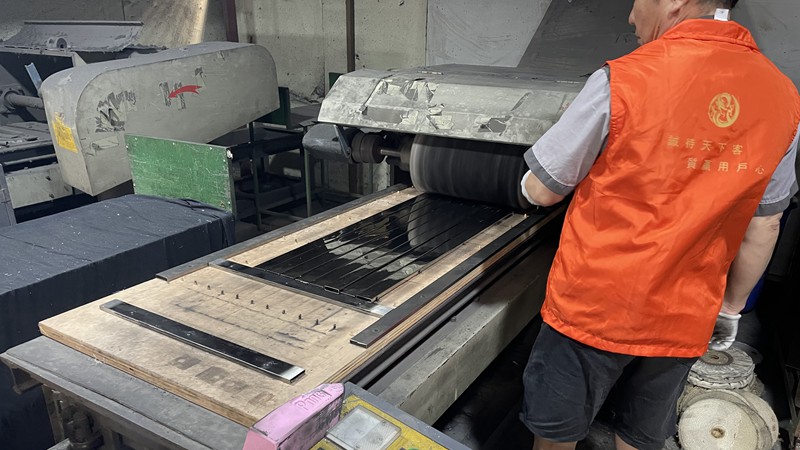
1. Mechanical polishing
Mechanical polishing is by cutting, material surface plastic deformation to remove the convex part of the polished and get a smooth surface polishing method, the general use of oil stone, wool wheel, sandpaper, etc., mainly by hand, special parts such as the surface of the rotary body, can use the rotary table and other auxiliary tools, the surface quality requirements of high can be used to ultra-precision polishing method. Ultra-precision grinding and polishing is the use of special abrasives, containing abrasives in the grinding and polishing fluid, pressed on the surface of the workpiece being processed, for high-speed rotary motion. Using this technology can achieve Ra0.008μm surface roughness, is the highest among various polishing methods. Optical lens mold often use this method.
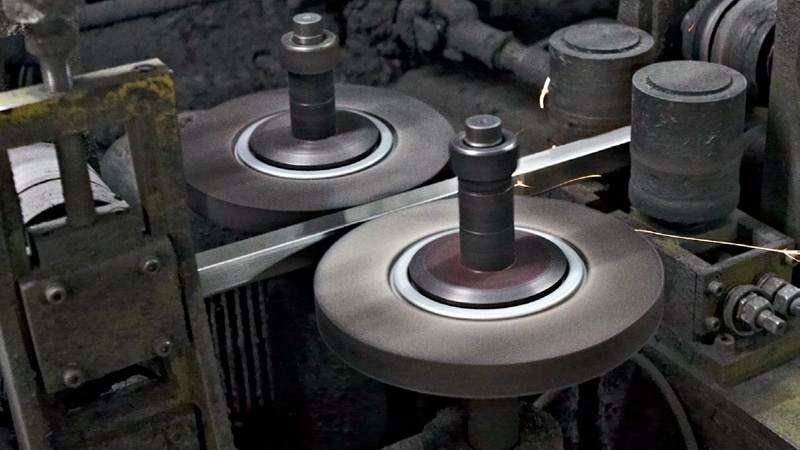
2. Chemical polishing
Chemical polishing is to let the material in the chemical medium surface microscopic convex part than the concave part of the priority dissolution, so as to get a smooth surface. The main advantage of this method is not complex equipment, can polish the shape of complex workpieces, can polish many workpieces at the same time, high efficiency. The core problem of chemical polishing is the preparation of polishing solution. Chemical polishing to get the surface roughness is generally a few 10μm.
3. Electrolytic polishing
The basic principle of electrolytic polishing is the same as chemical polishing, that is, by selective dissolution of the material surface tiny projections, so that the surface is smooth. Compared with chemical polishing, can eliminate the impact of cathodic reaction, the effect is better. Electrochemical polishing process is divided into two steps: (1) macro-leveling dissolution products to the electrolyte diffusion, the material surface geometric roughness decline, Ra>1μm.(2) micro-light leveling anodic polarization, surface brightness increase, Ra<1μm.
4. Ultrasonic polishing
The workpiece is put into the abrasive suspension and placed in the ultrasonic field together, relying on the oscillation of ultrasonic waves to make the abrasive grinding and polishing on the surface of the workpiece. Ultrasonic processing macro force is small, will not cause deformation of the workpiece, but the tooling production and installation is more difficult. Ultrasonic processing can be combined with chemical or electrochemical methods. On the basis of solution corrosion, electrolysis, and then apply ultrasonic vibration to agitate the solution, so that the workpiece surface dissolution products from the surface, corrosion or electrolyte near the surface evenly; ultrasonic cavitation in the liquid can also inhibit the corrosion process and facilitate the surface brightening.
5. Fluid polishing
Fluid polishing is to rely on the high-speed flow of liquid and the abrasive particles carried by the workpiece surface to achieve the purpose of polishing. Commonly used methods are: abrasive jet processing, liquid jet processing, fluid power grinding, etc. Fluid power polishing is driven by hydraulic pressure, so that the liquid medium carrying abrasive particles flowing over the surface of the workpiece at high speed reciprocally. The medium is mainly used in the lower pressure flow through the good special compounds (polymer-like substances) and mixed with abrasives, abrasives can be made of silicon carbide powder.
6. Magnetic grinding and polishing
Magnetic grinding and polishing is the use of magnetic abrasives in the magnetic field under the action of the formation of abrasive brushes, grinding and processing of the workpiece. This method has high processing efficiency, good quality, easy to control the processing conditions, and good working conditions. Using suitable abrasives, the surface roughness can reach Ra0.1μm.
7. Chemical mechanical polishing
Chemical mechanical polishing technology combines the advantages of chemical and mechanical grinding, is now the most commonly used polishing method, even cell phone cases, take the card pin, keys, etc. are polished with Jin Xin plane grinding machine. It can guarantee the efficiency of material removal while obtaining a more perfect surface, and the flatness obtained is 1-2 orders of magnitude higher than simply using these two kinds of grinding, and can achieve surface roughness from nano-level to atomic level. And the mirror effect out of polishing is very high brightness, no fault and good flatness. Generally with Jinxin plane grinding machine can achieve fast and good results.